Quality improvement programs aren’t a new concept or late-breaking fad in operations management. Companies have been using methods such as total quality management (TQM) and statistical process control (SPC) for decades. These traditional quality improvement initiatives have turned into what’s become known as Six Sigma quality.
Multiplied failures
Most companies typically operate their process at a 3 sigma quality level. This means that the process mean is 3 standard deviations away from the nearest specification limit, which defines the boundaries of a good part.
1 percent of the output of a 2.6 sigma process will be defective, assuming a normal distribution. By increasing the quality level to 3 sigma, you can reduce the defective rate to 0.3 percent. Even at this level, a company can lose a significant amount of profits, because 3 of every 1,000 products it makes have a defect.
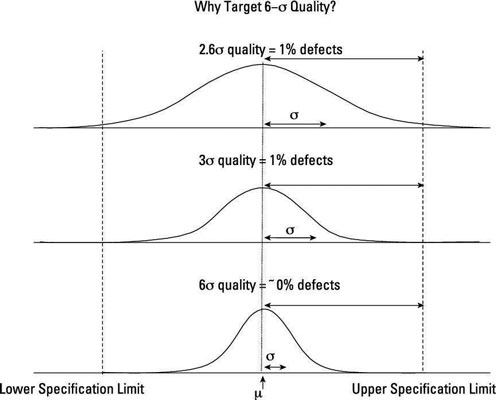
Realizing that 3 sigma just wasn’t good enough, the Motorola Corporation embarked on a quality journey starting in 1985, which led to the birth of what’s now called Six Sigma. Other companies picked up on the concept, and a quality revolution was launched in the world of business operations.
Because most products are assembled from multiple components, the quality level of each component is critical; each one has a compounding influence on the quality of the end product. This means that the expected quality of the end product diminishes as the number of components increases. You can calculate the expected quality of a product using this equation:
% Defective products = 1 – [1 – (% Defective/100)]Number of components
For example, operating at 3 sigma quality for each of 10 components that make up a final product may sound like a reasonable quality level, because only approximately 0.3 percent of each component will be defective.
But the expected end quality of the final product when the 10 components are assembled is only 97 percent; 3 percent of the final products are defective. This only gets worse as the number of components increases; here, each component is at a 3 sigma quality level.
Number of Components | Defective Rate of Final Product |
---|---|
200 part DVR | 45% |
500 part laptop computer | 78% |
3,000 part automobile | Approximately 100% |
Raise the bar
Six Sigma emphasizes this set of values:
Achieving quality improvement requires participation across the organization.
The process characteristics must be measured, analyzed, improved, and controlled.
To achieve high quality, a company must focus on continuous improvement.
Here are the fundamentals that separate Six Sigma from its predecessors and living relatives:
Efforts to improve quality are prioritized by return on investment. Projects are selected based on a cost-benefit analysis.
Decisions are made on concrete, verifiable data. Great attempts are made to remove qualitative assertions.
Implementation is handled by experts of different degrees with formalized training.
An increased emphasis is placed on benchmarking competitive performance.
The Six Sigma concept applies an increased focus on concrete results that can be measured. Improvement projects are chosen based on the potential financial results the organization can achieve. All improvement is measured and documented. The firm’s attention is squarely trained on actions that produce tangible results when Six Sigma is in action.
Varying skill levels
Perhaps one of the greatest differences that separates Six Sigma from other quality improvement programs is its emphasis on differentiated skill levels among employee training. Following the structure of martial arts training, Six Sigma uses a belt color system to designate the level of training the employee has received in the methods of Six Sigma:
Black belts: At the top of the skill chain are the black belts. These employees are highly trained experts and are responsible for leading Six Sigma projects. In many organizations, the mission of implementing the projects and training others is their full-time position.
Green belts: Next in line are the green belts. Although not experts, they’re proficient in Six Sigma methodologies and are part-time participants in the implementation effort.
Yellow belts: Yellow belts make up the majority of a Six Sigma project team. These are often the people who actually perform in the process being improved. The success of any project rests on the shoulders of these people because they not only work to improve the process but also maintain the gains after the others move on to their next project in the continuous improvement cycle.
Implementation of a Six Sigma initiative starts in the executive suite. Upper management must be fully committed to the program. Champions of the cause in upper management are usually tasked to oversee implementation of chosen projects. While upper management may not be black belts, they do require some understanding of the dedication required to successfully implement Six Sigma in their organization.