Businesses that manufacture products must determine how to calculate their product costs. Because most businesses produce multiple products, their accounting systems must be very complex and detailed to keep accurate track of all direct and indirect (allocated) manufacturing costs.
The basic equation for calculating product cost is as follows (using the example of the manufacturer given in the figure below):
$91,200,000 total manufacturing costs ÷ 120,000 units production output
= $760 product cost per unit
The equation shown above looks pretty straightforward, doesn’t it? Well, the equation itself may be simple, but the accuracy of the results depends directly on the accuracy of your manufacturing cost numbers. The business example shown in the image manufactures one product. Even so, a single manufacturing process can be fairly complex, with hundreds or thousands of steps and operations.
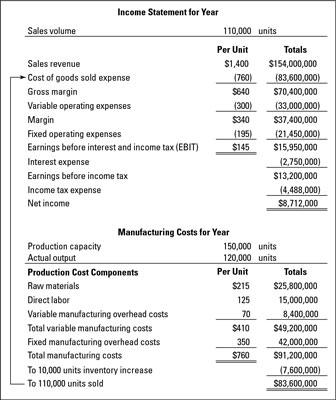
In the example, the business manufactured 120,000 units and sold 110,000 units during the year, and its product cost per unit is $760. The 110,000 total units sold during the year is multiplied by the $760 product cost to compute the $83.6 million cost of goods sold expense, which is deducted against the company’s revenue from selling 110,000 units during the year.
The company’s total manufacturing costs for the year were $91.2 million, which is $7.6 million more than the cost of goods sold expense. The remainder of the total annual manufacturing costs is recorded as an increase in the company’s inventory asset account, to recognize that 10,000 units manufactured this year are awaiting sale in the future. In the figure, note that the $760 product cost per unit is applied both to the 110,000 units sold and to the 10,000 units added to inventory.
The product cost per unit for the example business is determined for the entire year. In actual practice, manufacturers calculate their product costs monthly or quarterly. The computation process is the same, but the frequency of doing the computation varies from business to business.
Product costs likely will vary each successive period the costs are determined. Because the product costs vary from period to period, the business must choose which cost of goods sold and inventory cost method to use. (If product cost happened to remain absolutely flat and constant period to period, the different methods would yield the same results.)