In a process, some operations can process multiple flow units at a time and others can’t, so it’s important to analyze the operation batch size to maximize the total system’s capacity. To accommodate other operations in a process, a particular operation’s batch size may be lower than its maximum possible output.
By definition, no setup time is required between operation batches. In this analysis, assume that the operation batch size is the same as the transfer batch size, meaning that the units processed in any one cycle of an operation move on to the next operation as a batch at the same time.
Here are the general steps for determining optimal batch size to maximize process capacity:
Determine the capacity of each resource for different batch sizes.
Calculate the capacity for several batch sizes, including the minimum and maximum allowable size.
Determine whether the bottleneck changes from one resource to another.
The bottleneck may shift if some resources have the same cycle time regardless of batch size and others have changing cycle times based on batch size.
The operation’s cycle time is for a batch of parts, not just a single unit.
Determine the batch size that causes the bottleneck to change.
In general, this occurs when the capacity of the original bottleneck equals that of the new bottleneck.
Note the capacity of each resource for various batch sizes:
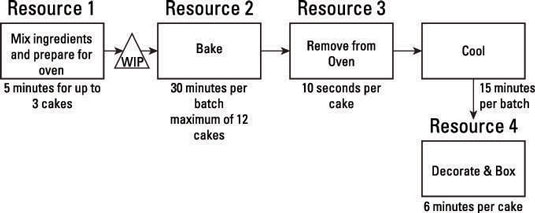
Resource 1 mixes the ingredients and prepares the pans for the oven. This resource can mix up to 3 cakes in 5 minutes, but he doesn’t necessarily need to make 3 at a time. Making only 1 or 2 still takes him 5 minutes.
After preparing the cakes for the oven, Resource 1 places them in a holding area (WIP), where they wait for the oven to become available.
Resource 2 (the oven) takes 30 minutes to bake a batch of cakes, no matter how many cakes are in the oven. The oven can hold 12 pans (maximum operation batch size is 12), and all the cakes must be put in the oven at the same time.
After the 30-minute bake time, Resource 3 removes the cakes from the oven and places them on cooling racks. Doing so takes her 10 seconds per cake. Resource 3 isn’t the bottleneck in this process because she needs only 2 minutes to process the maximum batch size of 12.
Each cake must cool at least 15 minutes before moving on to Resource 4, who removes each cake from the cooling rack, takes it out of the pan, brushes a glaze over the warm cake, and boxes it — at a pace of 6 minutes per cake. Cooling is an operation and not a WIP because Resource 4 can’t decorate a hot cake.
The batch size in this process can range from 1 to 12 cakes, the capacity of the oven. The chosen batch size determines the process capacity and flow time.
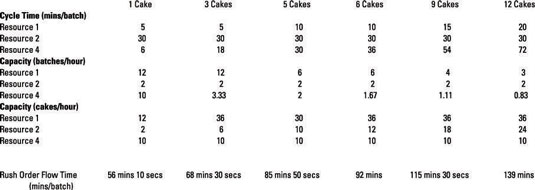
Comparing the capacity of each resource as batch size increases, the oven remains the bottleneck until batch size reaches 5 cakes. At this size, Resource 4 also becomes a bottleneck, and Resource 2 and 4 have a capacity of 10 cakes per hour. When the batch size exceeds 5, Resource 4 becomes the sole bottleneck — cakes will back up because cakes arrive faster at Resource 4than she can process them.
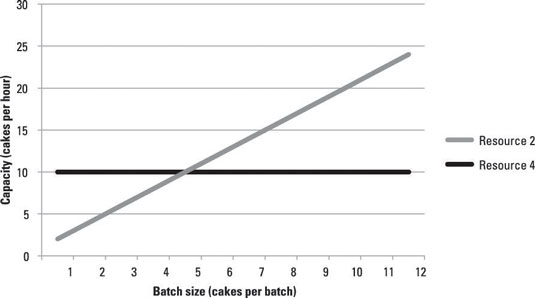
The optimal batch size is 5 cakes; this is where both Resources 2 and 4 have the same capacity.
When choosing the batch size, metrics other than system capacity may influence your decision. For example, the rush order flow time increases as batch size increases. If a smaller flow time is important to your customers, then you may want to reduce the batch size.
Likewise, quality expectations can also influence batch size. In the cake example, if the batch size is 5, then the last cake will wait an additional 24 minutes beyond the 15-minute cool time before Resource 4 can decorate it. If this additional time allows the cake to cool too much for the glaze to spread, then you may have to reduce the batch size.