The transfer batch size refers to the number of units in operations management that move as a group from operation to operation. On a process map, the transfer action is represented as an operation even though it doesn’t add value to the end product because the step is necessary for the parts to move through the process.
Here is a process that utilizes transfer batches. The process consists of three operators and one driver. The driver performs both of the transfer operations.
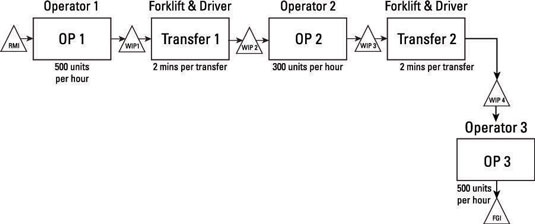
In this process map, each operation has its own waiting station for work in process (WIP). Each operation uses WIP as an input and outputs WIP to a different location. For example, OP1 processes parts into WIP1, and OP2 pulls parts to work on from WIP2. When WIP1 reaches the transfer batch size, it moves and becomes WIP2.
The following steps are useful when establishing transfer batch sizes:
Determine the bottleneck of the process, assuming a transfer batch size of one.
Initially, don’t worry about the resources used for transporting the batches from operation to operation. The amount of time these resources are utilized depends on the number of trips they have to make. As the batch size increases, they make fewer trips.
Decide on your material release policy, or how fast you allow parts to enter the process.
If you’re lucky and demand exceeds capacity, you’ll operate at the speed of the bottleneck to prevent overproduction. If demand is less than capacity, you’ll operate at the rate of demand. Also, consider seasonal demand, when you may want to produce more than current demand indicates. Assume that demand is greater than capacity and that parts enter the process at the rate of 300 units per hour.
Figure out the capacity (trips per hour) of your transportation resources.
In the example, moving a batch of parts from operation to operation takes 2 minutes. This means that the driver can make 30 trips per hour. Because there’s only one driver, he must divide his time between two transfer points. The number of transfers at each point doesn’t necessarily need to be the same.
Determine the minimum batch size that the transportation resources can accommodate.
Assuming that you maintain the same transfer batch size throughout the process, the driver can make up to 15 (30 ÷ 2) transfers per hour at each transfer point. Because 300 parts are released into the system per hour, the minimum batch size that the driver can process is 20 parts (300 ÷ 15). A smaller batch size requires more transfers and exceeds the capacity of the driver.
Set the batch size to meet your operational objectives.
When choosing batch sizes, you must consider many factors, such as operator work patterns, desired inventory levels, the time it takes to get through the process, facility layout, and traffic patterns within your facility.
Not all the transfer batches in a process have to be the same size.
Resource utilization
Small batch sizes tend to smooth the workload of an operation. If 15 batches of 20 units enter the system every hour — meaning that a batch arrives at OP1 every 4 minutes (60 minutes ÷ 15 batches) — then Operator 1 works for 2.4 minutes (60 ÷ 500) to process the batch.
He then waits for 1.6 minutes for the next batch to arrive to him. This means Operator 1 works for 2.4 minutes out of every 4 minutes, or 60% of the time.
On the other hand, large batch sizes generate longer continuous active periods followed by longer continuous inactive periods. If the batch size is 300 per hour and all the units arrive at the same time, Operator 1 works for 36 minutes to process all the parts and is then inactive for the rest of the hour, until the next batch of 300 units arrives to him.
The operator’s utilization remains at 60%, but he now has larger blocks of working time and downtime.
Flow time
Small batch sizes reduce the time for a batch of parts to get through a system. For example, OP1 and OP3 each requires 2.4 minutes to process 20 parts; OP2 can process a part every 0.2 minutes, taking 4 minutes to process 20 parts.
Summing the time the batch spends at each operation and adding 4 minutes for the two transfers, a batch of 20 units takes 12.8 minutes to process from start to finish, not including any wait times if they exist.
Conversely, large batch sizes increase the time a batch spends in the process. A batch of 300 parts goes through the process in 136 minutes: 36 minutes + 2 minutes + 60 minutes + 2 minutes + 36 minutes.
Facility traffic and inventory storage
Small batch sizes usually create more traffic in a facility because more transfers occur. In some situations, this may be dangerous and undesirable.
Small batch sizes result in less wait time for an individual part, which results in less WIP inventory.