A number of significant trends in manufacturing technology (ten of them, actually) are listed here along with an explanation of why they are important to you and your career as a fabricator, welder, machinist, or wherever the winds of manufacturing take you.
Join the Revolution
Anyone who’s anyone has heard of the Industrial Revolution, even those of us who were kicked in the shin for falling asleep during history class. But it turns out there’s a new revolution underway, one that promises to deliver much more than steam engines and electric lights. It’s called Industry 4.0, and unlike the revolutions of yore, it’s built on something we can’t see or touch: data. That’s because data (some people call it Big Data, because there’s so much of it available) is the main driver behind the Internet of Things, also known as the IoT.If you’ve gone shopping at an electronics store recently, you know that the IoT is bringing us a host of smart devices that promise to change the way each of us functions each day. That’s because our refrigerators can now tell us when we’re out of orange juice and will soon be able to order it for us as well. Our thermostats know our work schedules and automatically kick up the air-conditioning before we step through the front door. Siri knows our favorite brand of toilet paper. Google Home tells you when you forgot to pick up the kids from band practice. Alexa sings an off-key Happy Birthday on command. And self-driving cars? They’re coming, people.
What’s all this have to do with fabricating? Simple. All these advanced technologies affect the way we manufacture things, never mind the fact that smart cars, smartphones, smart refrigerators, and smart kiosks at the shopping mall place increasing demands on the folks who make these devices — that is, manufacturers. And just as they do in the kitchen or during the drive to work, the electronic sensors used on the production floor collect data and use it to make the lives of their human masters more efficient.
To manufacturers, the IoT has an extra letter: IIoT. It means the Industrial Internet of Things. What’s the difference? Actually, they’re like peas and carrots. Both rely on sensors embedded in network-capable devices that are able to provide massive amounts of data, information useful for trend-spotting and analytics. And the IoT and IIoT both offer the promise of increased efficiency, reduced costs, and greater product reliability, except that the latter is concerned only with industrial processes. Think self-driving forklifts instead of self-driving cars.
Most machine tools are way smarter than the Internet-capable light bulbs you installed in the living room last month. They’re able to monitor bearing temperatures, vibration, stamping and bending forces, motor loads, and a bunch of other electromechanical and physical characteristics that affect how the machine functions, then report back that information to the server in the front office or a datacenter sitting thousands of miles away.The software sitting on that computer can then analyze and display what’s going on to whoever wants to know. This might be the machine programmer, who can adjust laser power for more efficient cutting. It could be George, the maintenance dude, who needs to know if there’s a problem with a bearing or slide. And then there’s that nosy company accountant, who wants to know what job was worked on and why it was less than profitable. Or it might be the production manager, who needs to be alerted when the machine is idle so she can help out the operator (or yell at him to get back to work).
Cruise the Clouds
The IIoT wouldn’t exist without cloud computing, perhaps the most important leg of the Industry 4.0 stool. If you’ve been roughing it Ted Kaczynski–style in a secluded cabin for the past several years, you might be wondering about this term right now, but anyone with a smartphone or a computer touches the cloud every day.What is it? If you shared embarrassing pictures of your friend’s birthday party on Facebook recently, you used cloud computing. The same is true for subscribers to Shutterfly, Google Drive, and Amazon Prime Video, as well as those sharing three-dimensional (3D) computer-aided design (CAD) models on collaboration sites. Several of them exist and they’re a great way to see what others are doing — just Google “CAD sharing sites” and start surfing.
Whatever you do with it, there’s nothing too fancy about the cloud, really. Just stick a bunch of servers in a datacenter (a big temperature- and humidity-controlled room with an awesome Internet connection), set up a secure way for people to access them (firewalls, passwords, encryption, oh my), then hire a bunch of highly-paid computer geeks to play Robot Unicorn Attack while pretending to keep tabs on them. And here you thought the cloud meant those fluffy things that block the sunlight and drop rain at inopportune times.
Go Green
A hunk of ice the size of Delaware fell into the ocean recently. Oceans have become 30 percent more acidic since the start of the Industrial Revolution. Tucson just had the hottest year on record — for the fourth year in a row (as have other parts of the country). And while a sizable number of skeptics continue to believe that global warming is a hoax or at least unproven, few among us would argue with the notion that pollution and wastefulness are bad, and that lowering our collective carbon footprint is a worthy goal.An increasing number of machine-tool builders think so. Not only are their products becoming more energy efficient, but so are their factories — a few of them have been built from the ground up recently with the environment in mind. To shops that are focusing their energies on getting parts out the door, the energy consumed by their computer numerical control (CNC) machines is probably a distant concern; who cares how many kilowatt-hours were used making them, as long as we meet the customer’s delivery date?
Still, electricity costs add up, especially for shops with dozens of press brakes and turret punch presses running around the clock. And if the shop maintains a constant air temperature and humidity level at all times (something all machine shops should do), the monthly bill is likely to give even the most spendthrift shop owner indigestion.
Perhaps you don’t have the cash right now to replace the shop’s energy hogs with electric press brakes and fiber lasers, but you might think about adding solar power to your building (there’s a lot of room up top). At the very least, keep your existing machines running in tip-top condition, no matter how old they are. Your electricity bill (and your productivity) will thank you.
Get Lighter
Going green also means dealing with new metals and materials. Thanks to government energy mandates the world ’round, automakers and aircraft manufacturers are charged with continuing reductions in fuel consumption and emissions. One of the favorite ways of accomplishing this is by making vehicles lighter.Fabricating shops generally don’t contribute directly to the lightweighting movement, although they definitely feel its effects, and often not in a good way. True, lighter cars use more parts made of easy-to-fabricate aluminum (yeah!), but they also use plenty of parts made of nasty-to-fabricate steel and in some cases superalloys.
But wait. How does a much-heavier-and-more-expensive-than-aluminum metal like dual-phase steel make cars lighter? Easy. Since this and similar alloys are stronger by volume than their traditional car-making counterparts, less of it can be used. A comparable situation is seen on the aerospace side, where an increasing amount of abrasive carbon fiber–based composite materials is used, as well as the usual aerospace suspects: titanium and Inconel, all of which are challenging materials to fabricate.
At the same time, suppliers to these industries are under relentless pressure to reduce costs, improve quality, and decrease lead times. Long story short, fabricators and machine shops alike must continue to improve their processes and adapt to an ever-changing materials landscape as planes, trains, and automobiles become more energy efficient.Get Lost on the Paper Trail
Since we’re on the sustainability topic, let’s talk about going paperless. Setting aside beautiful forests and clean, breathable air, there are many reasons to do so. This is just as true for manufacturers as it is for the fast-food restaurant across the street. Paper, quite simply, is dumb (except for the paper used to print For Dummies books, that is). Here’s why:- Cost avoidance: Here’s the big kahuna. Paper costs money. Not just the price paid for the acres’ worth of dead trees you have lying about, but also the cash spent on printers, toner cartridges, and the IT people to manage it all, not to mention waste disposal and shredding costs. Granted, electronic storage space isn’t free, but it’s much less expensive than the paper alternative.
- Disaster recovery: The factory burned down last night? Major bummer. Not only do you need to start rebuilding, but the in-process quality documentation, hand-written notes on job routers, marked-up packing slips — all gone. Isn’t it better to digitize all that paper and store it on a backed-up server (or in the cloud) before the fire trucks arrive? Doing so might just save the company.
- Document security: Most shops consider internal documentation such as part drawings confidential. Even if they don’t, it’s almost certain their customers do. What’s to prevent a disgruntled employee or corporate spy from walking off with reams of valuable information, ready for selling to the highest bidder?
- Revision control: Regardless of the manufacturing environment, product specifications often change. So, too, do work instructions, quality procedures, shipping dates, and so on. Updating this information is much easier if you don’t have to chase piles of paper across the shop floor.
- Saving space: Anyone who’s saved job travelers, shipping receipts, copies of invoices, and so on knows one thing: They take up a lot of room. And finding something in all those boxes? It’s going to take a while. Wouldn’t you rather have scanned copies of your important documentation tucked away on a password-protected hard drive (or again, stored in the cloud)?
- Searching and replacing: The customer just called. She wants to move from Revision A to Revision B on all of her assembly instructions. “Right away, Ms. Jones, no problem,” you say, but come to find out, that document is referenced on every drawing and work instruction in the plant. With paper, you’re looking at weeks of work and a lingering worry that you might not have found everything. The paperless factory? It’s a half-hour job.
- Document scanners, especially in the shipping and receiving area
- Software for generating portable document format (PDF) or equivalent files
- User accounts for the network, and maybe for the enterprise resource planning (ERP) or product data management (PDM) system
Once you’re done with all that, get rid of the printers, as there are sure to be a few of your team members who simply can’t live without paper — taking them away eliminates any temptation. It also cuts a lot of money from the IT budget (the IT manager might disagree, but it will). Sounds scary? Maybe so, although everyone probably thought the first CNC machine was scary, too.
Cut the Wires
Your paperless journey, not to mention many other aspects of today’s manufacturing landscape, becomes much easier when everything in the company is connected wirelessly. If you don’t already have a wireless network, you can start by hiring a professional to help you design and implement one. Don’t cheap out by picking up a couple of $50 routers from the local office supply store, as there’s no faster way to incite rebellion over the new paperless project than a weak Wi-Fi signal.View Machines Virtually
This one’s still on the science fiction side of the fence, but just barely. Last year, I bought one of those Google Cardboard virtual reality (VR) devices, the holographic thingy that’s supposed to clip to the front of a smartphone and let you peer inside like it’s some newfangled View-Master, giving the user a chance to ride virtual roller coasters and observe virtual Krakatoa eruptions. Sadly, I never got the darn thing to work. I caught a glimpse of a virtual T-Rex chasing a virtual Triceratops just before the strap broke, whereupon Google Cardboard fell to the ground and the lens shattered.My experience did, however, give me a great idea. What if fabricators could use VR headsets to peer into their machine tools? Maybe they could view work instructions and 3D CAD models, check the status of a stamping operation, edit a program, or stop a process, all from a remote display worn on one’s head and controlled with haptic gloves?
It turns out I’m not so crazy. Software providers such as Autodesk and Microsoft are looking at VR-enabled engineering systems. Ford Automotive uses VR to analyze its vehicle designs, and defense system manufacturer BAE Systems uses it to speed product development. Within the past few years, several universities have announced VR-based machine simulation projects, one of which suggests that CNC programs may one day be generated via hand gestures in a virtual reality world. Lastly, a leading workholding company recently announced a VR design solution for use in stamping applications. It might be a good idea to keep a virtual eye on this emerging technology.
Manufacture Additively
Some industry experts consider additive manufacturing, better known as 3D printing, to be the biggest hype of the century. After all, this now 30-something-year-old technology hasn’t become the dominant parts-making process as many early adopters prognosticated. The big promises have come to naught they say, and it’s unlikely 3D printing will have much of an impact on manufacturing within your lifetime, or in mine.After all, households the world over don’t have 3D printers in their kitchen, ready to whip up an ice cube tray or a cup of cappuccino (although a growing number of homeowners now have 3D printers in their garages and workshops). Auto repair shops aren’t printing up replacement parts as you pull in to the parking lot, and department stores aren’t producing bespoke tennis shoes and bedside tables (yet).
Nor have manufacturers embraced 3D parts printing as many thought they would, preferring instead to make parts the “old-fashioned” way (although an increasing number have purchased printers and are now testing the additive manufacturing waters). But pick up any trade publication or cruise the Internet for manufacturing news and you’ll see that a great deal has changed over the past few years. More than any other manufacturing technology, 3D printing has evolved by leaps and bounds since its inception, especially over the past decade or so. Where 3D printers were once capable of little more than conference room prototypes, there’s now little these machines can’t make, and do so in an increasingly cost-effective manner.
Granted, you won’t be 3D printing garden gnomes for your front lawn anytime soon. And the vast majority of parts for cars and airplanes will continue to be made using conventional techniques, at least until those modes of transportation are obsoleted by something better (teleportation, perhaps). Fasteners, folding chairs, Frisbees, and farm implements — anything very large, very high volume, or very cheap to make will remain, for the foreseeable future at least, firmly in the traditional manufacturing world.What will change is the production of those parts that are difficult or even impossible to produce via subtractive manufacturing processes (that is, machining and fabricating). That’s because additive manufacturing laughs at complexity. Printing parts that resemble spider webs, honeycombs, seashells, and a host of other “organic” shapes is about as difficult as getting greasy hands from a bowl of Movie Theater Butter–flavored microwave popcorn. As proof, check out the part in the figure.
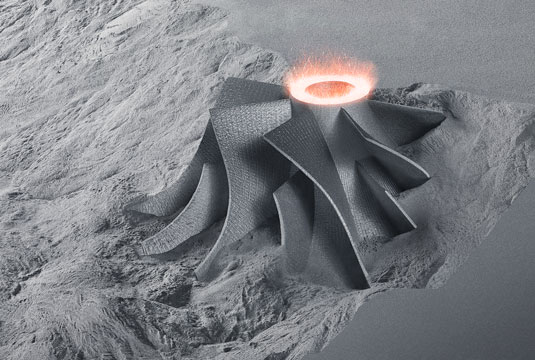
Compared to traditional manufacturing processes, complex parts like the turbine blade shown here are much easier to produce on a 3D printer.
Who cares about shapes like these? Why, anyone who wants to make parts that are stronger, lighter-weight, and easier to assemble does. Aircraft-engine manufacturers use 3D printing to reduce part counts in fuel-injector assemblies. Orthopedic surgeons use 3D printers to make patient-specific hip joints and cranial repair plates. Jewelers create custom belly-button rings and automakers prototype aerodynamic body parts with it.
And soon, well within your lifetime and mine, people will routinely be printing everything from circuit boards and custom-fit solar cells to apartment buildings and human body parts (the latter is already a reality using 3D bio-printers). For fabricators, this means low-cost fixtures and tooling, gages, prototypes and low-volume production of stamped metal parts, and more. Still think it’s all hype?
Embrace Automation
Shop-floor automation goes beyond a ready-to-serve fleet of droids. There are also automated press-brake tooling systems and flexible manufacturing systems (FMS) that allow press brakes, turret presses, and other fabricating equipment to run unattended for hours or even days at a time.At its core, automation is all about one thing: eliminating waste (something I dig into more deeply in the next section). In the case of material handling systems, waste is measured as machine downtime, but many other tools are available that can be used to eliminate various other forms of waste:
- Waste in the estimating process: Automated quoting software can eliminate the tedious calculations needed to determine machining time and manufacturing costs.
- Waste during programming: Semiautomated CAM systems, cloud-based tooling models, and manufacturing simulation software can help avoid crashes once the program has hit the shop floor.
- Waste during machine setup: Automated measuring equipment and RFID-enabled tooling can transmit important tool data directly to the machine control or relevant software systems. (Check out Figure 16-2 if you don’t believe me.)
- Waste on the shop floor: Waste that results from operators breaking up skeletons (the leftovers from many sheet metal operations) or moving parts from machine to machine can be avoided by spending a few bucks on automated parts conveyors and material handling systems.
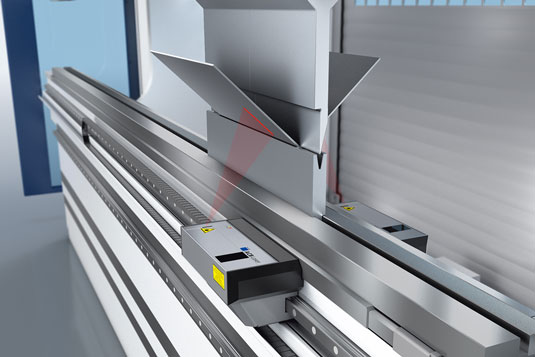
This press brake is equipped with a laser for measuring bend angles on the fly, greatly simplifying the setup process while improving part quality.
Additionally, there’s the waste of manual shop-floor data collection (eliminated with computers and barcode readers), waste caused by unexpected wear or breakage of fabricating tools (eliminated with tool-life management software and sound process control), waste of time spent measuring parts (eliminated with automated systems such as vision or coordinate measuring machines), waste in parts packaging … you get the idea.
Of course, robots and automated material handling systems will always be the big cheeses in any lights-out production environment, but it’s important to recognize that there’s more to the story than those electromechanical golems. Without supporting forms of automation, returns on investment in automated machine tools will be limited. The bottom line is this: Automation of any kind saves time (thus reducing waste). It’s automatic.
Lean Out Your Shop
Taking that waste discussion one step further, let’s talk about all that humans can do to eliminate it, something most experts agree is possible after implementing Lean manufacturing principles. Lean is nothing new.Many say it was invented shortly after World War II, when Japanese industrial engineer Taiichi Ohno, together with coworker Shigeo Shingo, developed the Toyota Production System (TPS). Others say Taiichi simply took Henry Ford’s assembly-line way of thinking to the next logical step.
Whatever the case, people have been attempting to increase the efficiency of their manufacturing processes since the days of Eli Whitney and the steam engine, and if you’re to become a valued fabricating citizen, you should attempt to do the same thing. It begins with eliminating the seven deadly sins of waste, which in Lean terminology is called “Muda.” These include:
- Waiting: Also known as work in process, or WIP, which to a manufacturer means partially completed parts waiting for the next operation.
- Overproduction: Making too many parts or parts that are too early for the customer’s needs.
- Rejects: This one’s a no-brainer; scrap or defective parts are bad for everyone involved.
- Motion: Unnecessary movement of people and machines, like walking too far for tools, and inefficient CNC programs.
- Processing: More specifically over-processing or fabricating to greater accuracy than required on the drawing.
- Inventory: Too much material, too little material, or material that is too late all cost a company money.
- Transport: Moving stuff around needlessly creates the risk of it being lost or damaged.
The fathers of Lean have all gone to the great factory floor in the sky, but many others have taken the Lean baton and run with it, and today Lean is an all-encompassing system of shop-floor improvement. It includes JIT (just-in-time) delivery of products, SMED (single-minute exchange of die), Kanban (pull-type scheduling), Six Sigma (defect reduction leading to process improvement), DFM (design for manufacturability), and much more.