In fact, in the last decade, data has emerged as the new currency that operates across all levels of commerce, right down to the consumer, who pays for the use of “free” social media platforms with their personal data, which those platforms exchange with their clients.
The combination of AI and analytics can help manufacturers optimize the use of their IoT data for many applications. Consider three related strategies: proactive replenishment, predictive maintenance, and pervasive visibility.
The following figure shows the relationship between the method of controlling costs and the AI technique used to accomplish it.
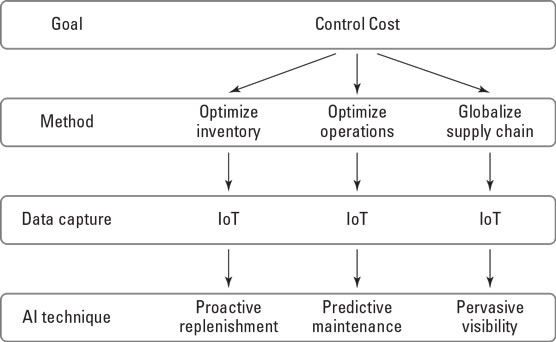
Connected supply chain
A supply chain connects a customer to the raw materials required to produce the product. It can be as simple as a single link, such as when the customer stops at a roadside stand to buy tomatoes directly from the farmer. Or it can be very complex and involve dozens of links, such as all the steps between a customer driving a car off the lot back to mining the iron ore or bauxite for the steel or aluminum engine block.In a traditional supply chain, each link operates as a black box, connected to each other by a paper-thin link made up of documents such as purchase orders, shipping manifests, invoices, and the like. Each entity does its own planning, forecasting, and ordering while being blind to conditions on either side of it in the chain.
You could think of the links in the traditional supply chain as separate continents, each with its own ecosystem but largely isolated and insulated from the ecosystems of other continents. A connected supply chain brings those continents together like the supercontinent Pangea in the Paleozoic era, forming one interconnected ecosystem of partners, suppliers, and customers.
In the connected supply chain, the paper-thin connection of the traditional model is replaced with a digital connection that provides full visibility in all directions.
A 2017 McKinsey study suggests that companies that aggressively digitize their supply chains can expect to boost annual growth of earnings by an average of 3.2 percent — the largest increase from digitizing any business area — and annual revenue growth by 2.3 percent.In a recent KRC Research survey of manufacturing executives, 46 percent indicated that big data analytics and IoT are essential for improving supply chain performance. They identified the two areas where big data analytics can have the greatest impact on manufacturing to be improving supply chain performance (32 percent) and enabling real-time decisions and avoiding unplanned downtime (32 percent).
The study also identified the top three benefits of big data for manufacturers:
- Enabling well-informed decisions in real-time (63 percent)
- Reducing wasted resources (57 percent)
- Predicting the risks of downtime (56 percent)
The connected supply chain enables you to react to changing market needs by sharing insights between every node in the value chain. There are many other applications for AI in manufacturing, some of which I address later, but the three elements of connected supply chain — proactive replenishment, predictive maintenance, and pervasive visibility — provide an intuitive case for using AI to revolutionize your business.
Proactive replenishment
Optimizing inventory levels while improving customer experience requires the ability to automate much of the replenishment process. Proactive replenishment leverages analytics to monitor inventory consumption and initiate a purchase order on the business network to the supplier to replenish the stock before an out-of-stock situation occurs. The intelligent and connected supply chain provides real-time inventory visibility. In addition to reporting stock levels, it can indicate the condition of each item — such as the temperature at which it is stored — to ensure the quality of those items. Manufacturers can automate the replenishment of parts from the supplier before they are needed in the production process. And, query between suppliers to procure from which has availability, the best rates, and taking into account shipping times required for in-time delivery.Predictive maintenance
The ability to predict when a part of a sub-system of a serviceable product is likely to fail and intervene can save a manufacturer millions of dollars, and thus predictive maintenance is a key investment area for the supply chain. Whether that part is within the production process, within the warehousing environment, or part of a connected vehicle, an IoT network automatically monitors and analyzes performance to boost operating capacity and lifespan. This system intelligently decides whether the part needs to be replaced or repaired and can automatically trigger the correct process, typically reducing machine downtime by 30 to 50 percent and increasing machine life by 20 to 40 percent. Studies by the Federal Energy Management Program of the U.S. Department of Energy found that predictive maintenance provides a 30 to 40 percent spending reduction compared to reactive maintenance, and an 8 to 12 percent spending reduction compared to preventative maintenance.Organizations often make incremental progress toward predictive maintenance, starting with monitoring IoT data in the control room and reacting to problematic readings. In the next stage, they run reports to view recommendations for maintenance. In the final stage, they remove the requirement for human interaction to initiate maintenance by automating the creation of repair tickets.
Pervasive visibility
Pervasive visibility is the ability to see exactly where goods are during their life cycle, providing a view of the current state of all assets across the entire organization and beyond to partners, customers, competitors, and even the impact of the weather on operations and fulfillment. IoT plays a key role in providing that visibility.Current estimates predict that there will be 75 billion connected devices by 2025, ten connected devices for every human on the planet. Most of those devices will be in the manufacturing sector. When you consider that a single device can produce gigabytes of information each minute, the volume and velocity of data within production and operations can easily spiral out of control — or, more often, simply be ignored.
While 60 percent of executives that McKinsey surveyed said that IoT data yielded significant insights, 54 percent admitted that they used less than 10 percent of that IoT information.
Making sense of that data is where AI comes in. By combining AI and analytics, you can bring together information from a variety of data sources, identify patterns and trends, and provide recommendations for future actions. It provides the basis for new levels of production and business process automation, as well as improved support for employees in their daily roles and in their decision-making.
To achieve these gains in the supply chain, AI has the potential to bring together both structured and unstructured data from a wide range of sources, including IoT devices, plant operations, and external partners to identify patterns linking factors such as demand, location, socioeconomic conditions, weather, and political status. This information forms a basis for a new level of supply chain optimization spanning raw materials, logistics, inventory control, and supplier performance and helps anticipate and react to market changes.