As with nylon (polyamide), the 3D printing technology prints a stainless steel model by binding together layers of ultra-fine grains of stainless steel powder in an inkjet-like printer. A layer of stainless steel powder is spread across the base of what is called a build box, and then a special print head moves back and forth over that layer, depositing a binding agent at specific points, as directed by a computer and your design file, such as a Tinkercad design. Once that layer is finished and has been dried with heaters, a new layer of powder is spread, and the process begins again. Layer by layer, your part is created.
Once the 3D printing is complete, the 3D model is carefully taken out, and any extra powder that was not bound is removed. The printed part is still fragile, and this green state is then followed by being sintered in an oven at 1300°C, in either sand or on a ceramic plate. Sand is used for designs that are irregular and don’t have a flat base, and the ceramic plate is used more often for technical pieces with a flat base.
After cooling, the 3D model is put into a mechanical polishing machine for finishing.
The Tinkercad materials guide states that stainless steel is a very strong 3D printing material. It is normally 3D printed in multiple steps or directly from a powder medium. It has various coloring options, including gold and bronze plating, and normally 3D prints to about six layers per 1mm and has a 3mm minimum wall thickness. This figure shows you some 3D stainless steels prints from the Tinkercad materials guide.
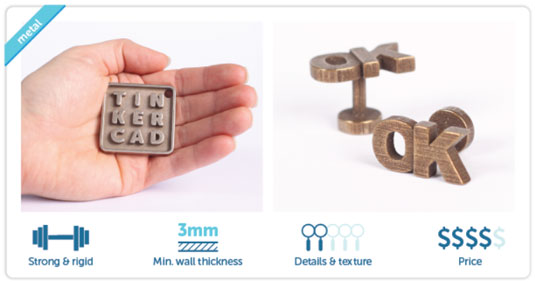