3D printing with titanium has many advantages over traditional manufacturing methods. When it comes to complexity of titanium 3D printed parts, titanium can produce complex shapes that otherwise may not be possible. This creates many design possibilities and parts optimization.
Titanium parts that are 3D printed always retain their mechanical properties when batch produced, reducing the need for welding, which can sometimes create impurities and areas of weakness in a design. It also reduces production time and gives increased flexibility because 3D printing takes away several of the traditional manufacturing steps, allowing parts to be produced (sometimes) in hours, not days.
Titanium is an expensive metal, and traditional methods can produce titanium waste, which can quickly increase raw material costs. 3D printing keeps waste to a minimum, which keeps raw material costs down. However, titanium 3D printing is still expensive. The 3D printing industry needs more innovation and invention to overcome these challenges and improve the 3D printing technology — for example, reducing the cost of titanium powder, which is used for 3D printing.
The Tinkercad materials guide classes titanium as the strongest material used for 3D printing. It is 3D printed using a process called Direct Metal Laser Sintering (DMLS), where an STL file is used by the DMLS operator to orientate the model geometry and add support structures where needed. Once this build file is complete, it is then sliced into the appropriate layer thicknesses for the 3D printing process to begin. DMLS uses titanium powder that is fused in to the 3D print by the laser. It can print up to 30 layers per 1mm and has an incredible 0.2mm minimum wall thickness. This figure shows you some 3D printed titanium designs from the Tinkercad materials guide.
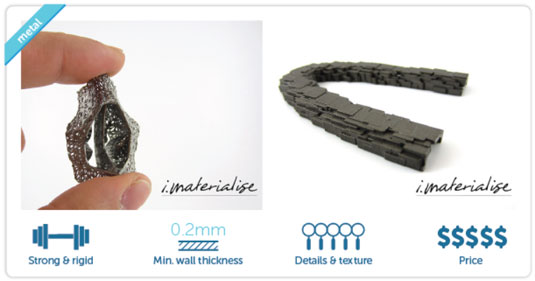