For one thing, increasing the amount of material that you order each time, called the lot size, also increases the amount of inventory that you have. You start with no inventory; then you receive a shipment of whatever lot size you agreed to purchase from your supplier. You gradually sell that inventory to customers until you have no inventory left. Eventually, you run out of inventory again. Over that period, how much inventory did you have on average? The answer is that the average amount of inventory — and the average amount of working capital that you had tied up in inventory — is half of your lot size. Therefore, on average, the more you order at one time, the more inventory you end up with. You can see how this works here.
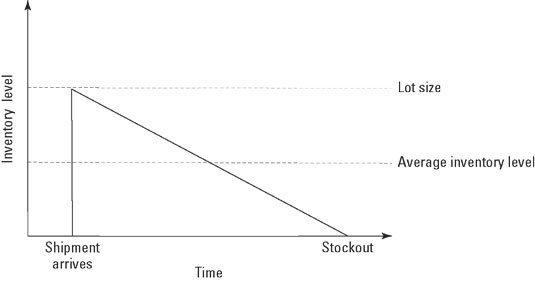
Ordering in larger quantities also means that you need to have extra space to store inventory and more people to manage it. Although increasing the lot sizes may get you a lower cost per unit, it could end up increasing your inventory costs even more.
A similar problem comes up when you consider suppliers located farther away. The price per unit may be lower, but the increased transportation costs can eat up all those savings and then some. Shipping items a longer distance can also force you to buy in larger quantities. The farther you have to move something, the more things can go wrong along the way. To compensate for this risk, you'll probably need to — yep, you guessed it — increase inventory.
The way to balance the priorities of purchasing and logistics is to take a total-cost analysis approach to sourcing decisions. Make sure that you're evaluating all the elements that will cost your supply chain money. You may find that a nearby supplier that can deliver in small batches and at a low transportation cost is a much better option than a lower-cost supplier in a distant location that would require you to spend more money on transportation and inventory.