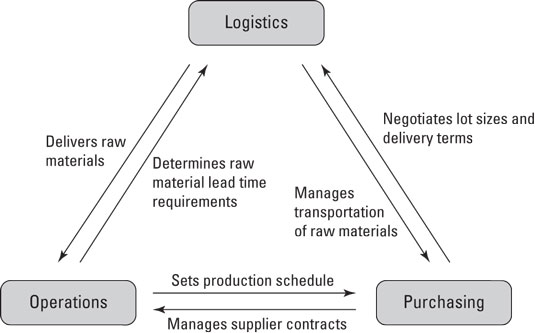
The purchasing, logistics, and operations teams often have conflicting goals without realizing it. Managing these functions independently leads to poor overall performance for your company. Supply chain managers need to make sure that the objectives of these groups are aligned in order for the company to meet its top-level goals.
The simplest top-level goal for many supply chain decisions is return on investment. Focusing on this one objective can often help everyone see the big picture, and look beyond the functional supply chain metrics such as capacity utilization or transportation cost.
Purchasing in supply chain management
Purchasing (or procurement) is the function that buys the materials and services that a company uses to produce its own products and services. The basic goal of the purchasing function is to get the stuff that the company needs at the lowest cost possible; the purchasing department is always looking for ways to get a better deal from suppliers. Some of the most common cost-reduction strategies for a purchasing manager are- Negotiating with a supplier to reduce the supplier's profit margin
- Buying in larger quantities to get a volume discount
- Switching to a supplier that charges less for the same product
- Switching to a lower-quality product that's less expensive
Your total costs include all of the investments and expenses that are required to deliver a product or service to your customer.
Logistics of supply chain management
Logistics covers everything related to moving and storing products. This function can go by different names, such as physical distribution, warehousing, transportation, or traffic.Inbound logistics refers to the products that are being shipped to your company by your suppliers. Outbound logistics refers to the products that you ship to your customers.
Logistics adds value because it gets a product where a customer needs it when the customer wants it. Logistics costs money, too. Transporting products on ships, trucks, trains, and airplanes has a price tag. Also, whether a product is sitting on a truck or gathering dust in a distribution center, the product is an asset that ties up working capital and probably depreciates quickly. The goals of the logistics function are to move things faster, reduce transportation costs, and decrease inventory. Following are some ways that a logistics department might try to achieve these goals:
- Consolidating many small shipments into one large shipment to lower shipping costs
- Breaking large shipments into smaller ones to increase velocity
- Switching from one mode of transportation to another, either to lower costs or increase velocity
- Increasing or decreasing the number of distribution centers to increase velocity or lower costs
- Outsourcing logistics services to a third-party logistics (3PL) company
Operations of supply chain management
The third function that is key to supply chain management is operations. Operations is in charge of the processes that your company focuses on to create value. Here are some examples:- In a manufacturing company, operations manages the production processes.
- In a retailing company, operations focuses on managing stores.
- In an e-commerce company or a 3PL, the operations team may also be the logistics team.
- Reducing the amount of capacity wasted due to changeovers and maintenance
- Reducing shutdowns for any reason, including those caused by running out of raw materials
- Aligning production schedules and orders for raw materials with forecasts received from customers