Fortunately, an early turret lathe came along in 1861, produced by the Lamson Goodnow and Company (see the following figure), which at that time was operating in the old Robbins and Lawrence armory in Windsor, Vermont. Its new mechanism made tool changes much faster and easier than on previous lathe designs. Nearly 30 years later, James Hartness took the turret ball and ran with it, designing a flat turret lathe that greatly increased the efficiency of turning operations.
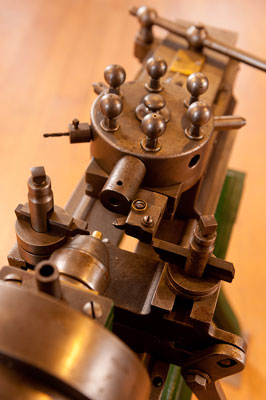
This 1861 turret lathe from Lamson, Goodnow and Co., shares a number of similarities with Maudslay's original screw-cutting lathe design. If you want to see it in person, head on over to the American Precision Museum in Windsor, Vermont. Tell them Kip sent you.
Today virtually every CNC lathe — and some manual turning machines — have a turret able to carry 8, 10, 12, or more cutting tools. If yours doesn't, no worries: Just replace the standard "tool post" with a quick-change, wedge-lock style toolholder (Aloris is one) to make tool changes fast and accurate.
You can equip your manual milling machine with a similar device: the power draw bar, which eliminates the tedious wrench-turning that's otherwise needed to attach toolholders to the mill's spindle. And machining centers? Why, an automatic tool changer, or ATC, is one of the defining features of these machines. Most can hold a dozen or more tools in a carousel mounted alongside the spindle, although some carry hundreds of tools in a "beehive" or chain-driven magazine. Give the machine the proper command and watch as the arm comes in, grabs the old tool, and puts in a replacement faster than you can say, "I love automatic tool changers."