There are countless ways for an operations manager to design a process. What constitutes a good or bad design depends on what your objectives are. Some general rules of thumb can help you maximize your process design and achieve your goals.
Consider the effects of the placement of activities in the process. Serial processes have operations that must occur one after the other; parallel processes can occur simultaneously.
A serial process
In a system with a serial process design, activities occur one after the other; no activities occur simultaneously. Here is a typical serial process in which activities take place one at a time in a defined sequence. A resource performs an operation and places the output in a waiting area until the next operation is ready to receive it as an input. The part or customer is the flow unit.
In this serial process, the resource performing OP1 has the smallest capacity and is the bottleneck with a capacity of one flow unit per day. The time it takes one flow unit to get through the system is two days (one day for OP1 and a half day each for OP2 and OP3).
Because this calculation does not include any wait times, it’s really a rush order flow time and not the actual flow time. But for simplicity, think of this variable as the flow time.

A major problem with a serial process is that the flow time can be very long; after all, the flow unit must go through the system one step at a time. It may be possible to reduce flow time if you can identify where in the process operations can happen simultaneously. Operations that happen at the same time are said to be in parallel.
Place operations in parallel
Placing two or more operations in parallel, a term that indicates operations perform their functions at the same time, can either reduce flow time or increase capacity, depending on whether the parallel operations perform different functions (unlike operations) or perform the same function on different parts (like operations).
Placing unlike operations in parallel reduces the flow time but doesn’t impact capacity. Placing like operations in parallel increases the operation’s capacity — and the system capacity if the operation is the bottleneck — but doesn’t affect the flow time.
Unlike operations
Multiple operations that perform different processes on the same flow unit at the same time are referred to as unlike operations. For example, a cashier at a fast-food restaurant can take your money at the same time the fry cook is preparing your order.
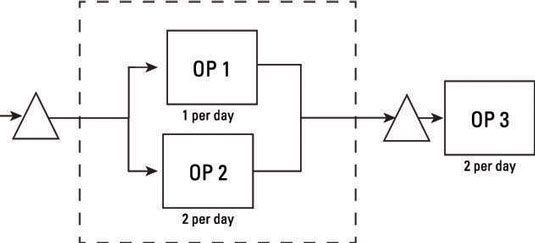
OP1 and OP2 are completed at the same time, but both operations must be completed before the flow unit can proceed to OP3. The capacity of the bottleneck stays the same, so the system capacity remains one per day, but the flow time is reduced.
When unlike operations are parallel and both must be completed before the flow unit can proceed, the flow time for the pair is the greater of the two. So, the slowest one is the pace setter. The flow time decreases by the 0.5 days of OP2 because this operation begins and ends inside the time it takes to complete OP1; total flow time for the process is now 1.5 days.
You can place unlike operations in parallel for the same flow unit only if they can work on the flow unit at the same time. For example, operations that attach each of four different doors and the hood of a car in assembly can be placed in parallel.
But you can’t attach a door to a car in assembly at the same time the flow unit (the car) is going through the paint booth unless you also desire to paint the equipment and operators.
Like operations
When like operations are in parallel, more than one of the same type of resource is performing the identical operation but on different flow units. In a restaurant, for example, several servers take orders from different customers. In this case, the servers are functioning in parallel.
Adding like operations in parallel to a system usually requires adding equipment or an employee to the process. Because the bottleneck determines system capacity, if your goal is to increase capacity, you only want to add resources to the bottleneck operation because adding them to another operation won’t change capacity.
A flow unit is now positioned at each of the OP1 stations. Because OP1 was the bottleneck, the system capacity is increased. You now have two resources, each producing one per day, making the new capacity two per day.
OP1 now has the same capacity as OP2 and OP3. You’ve effectively balanced the production line! Now, all operations can be considered a bottleneck; to improve capacity any further, you need to take action on all three of the bottlenecks.
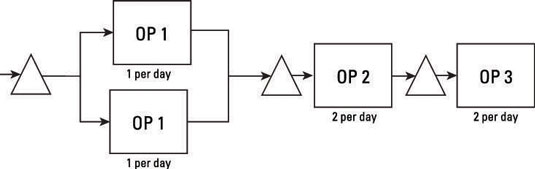
Although you increased the system capacity, the flow time — the time needed to get one unit through the entire process — holds steady. Even though you have two resources performing OP1, they’re doing so on different flow units, and each flow unit still takes one day at OP1. Therefore, the flow time remains the same at two days.